Critical Components, Critical Challenges
In Bloomington, Indiana, MSP Manufacturing produces highly specialized components for the aviation industry—instrument cases, switch guards, and cooling vents that demand impeccable precision. Until recently, crafting such intricate parts required hours of manual programming for computer numerical control (CNC) machines, a task handled by a dwindling pool of seasoned technicians.
The shortage of skilled CNC programmers has long been a bottleneck. Programming a single part could take up to an entire day. “We had about three programmers,” recalls Johnny Goode, MSP’s president and COO. “And it was kind of a bottleneck.” That changed dramatically when Goode discovered a new AI-powered software from CloudNC at an aviation trade show. What once took 90 minutes could now be done in just seven—plus 15 minutes of operator tweaks.
"Going from 90 minutes to 22 minutes is a big deal, and we’ve seen that get even better as we’ve learned to use the software more." — Johnny Goode, President & COO, MSP Manufacturing
AI Meets the CNC Skills Gap
U.S. manufacturers are facing a critical shortage of skilled labor. A recent Deloitte and Manufacturing Institute study warns that 1.9 million U.S. manufacturing jobs could go unfilled by 2033 due to skills deficits—CNC programming among the hardest hit.
Nearly 70% of U.S. machinists are over 45, and younger generations remain skeptical. Just 14% of Gen Z respondents in a Soter Analytics survey said they’d consider manufacturing work, citing safety concerns and rigid work conditions. Compounding the issue, CNC programming demands years of training and leaves little room for error—mistakes can ruin expensive parts and equipment.
CloudNC’s cofounder and CEO, Theo Saville, has watched the crisis deepen over the past decade.
"There have been fewer machinists in industry every year for the last 35 years, give or take. The numbers keep going down, while the industrial production requirements keep going up." — Theo Saville, CEO, CloudNC
From Submarine Design to Manufacturing Disruption
Saville conceived CloudNC while a mechanical engineering student at the University of Warwick. During a human-powered submarine design competition, his team faced a 10-week delay waiting for machined parts. Ironically, the university’s CNC machines sat idle—off-limits without five years of training.
Frustrated by the outdated gatekeeping, and armed with a minor in computer science, Saville envisioned software that could automate CNC programming entirely. Eight years later, CloudNC’s AI software—Cam Assist—delivers on that promise.
Inside CloudNC’s AI Engine
CloudNC’s technology deconstructs CNC programming into 30+ distinct problems: material tolerances, tool paths, chip buildup, vibration, heat dissipation, machine torque, and more. Instead of using one massive AI model, CloudNC trains small models to solve each subproblem, orchestrated alongside traditional CAM software.
The system accepts 3D CAD files from programs like Autodesk or Siemens. It then runs thousands of potential machining strategies in seconds, discards inefficient paths, and generates the optimal instruction set. Operators load the code into machines via USB or network, then execute.
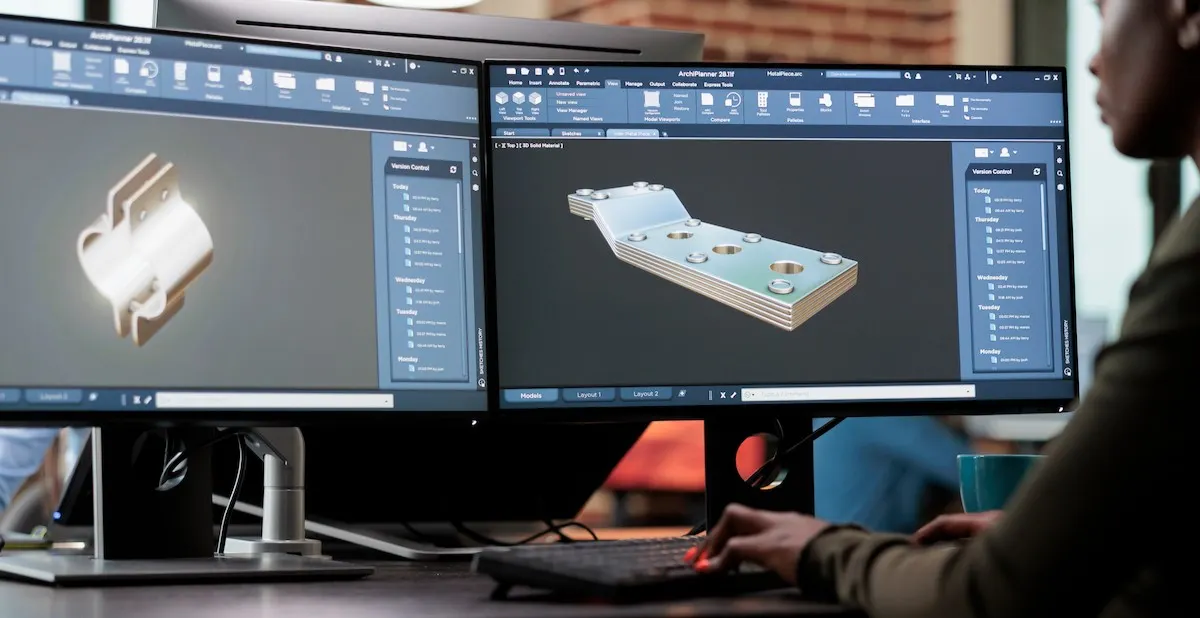
Building Intelligence from the Factory Floor
Gathering high-quality data remains a hurdle. CNC programming knowledge is often tribal—trapped in operators’ heads or scattered across incompatible systems. Even when manufacturers save successful part programs, few document failed attempts, which are crucial for training robust AI.
To overcome this, CloudNC runs its own mini-factory in Essex, England. The facility—staffed by just 15 people—produces real parts for paying clients, generating proprietary data to refine the software. The in-house shop gives CloudNC rare insight into both optimal and flawed machining strategies.
Rethinking Competition in Manufacturing
With CloudNC’s AI in place, MSP Manufacturing has dramatically improved turnaround times. Rush orders that once went unquoted now arrive and ship within days. “If they said less than three weeks, we wouldn’t have even quoted it before,” says Goode. Now, MSP handles mission-critical parts for Fortune 500 clients and even the U.S. Department of Defense.
The benefits aren’t just in speed. AI-enhanced programming has also boosted operator skills. MSP requires employees to manually program a part before using the software. The policy has unexpectedly spurred more workers to learn CNC programming.
Other startups are entering the space. U.K.-based Plyable focuses on AI for mold-making, while Switzerland’s Manukai targets broader CNC challenges. Meanwhile, Formlogic, a U.S. firm once connected to SpaceX, shuttered after failing to gain market traction.
One-Click Manufacturing: The Long-Term Vision
CloudNC’s commercial momentum is accelerating. The company now serves hundreds of small and mid-sized U.S. machine shops. While it generated $3 million in revenue last year, it also posted a $22 million loss, according to filings with the U.K.’s Companies House.
Still, backers remain bullish. CloudNC has raised $78 million to date from investors including Autodesk, Lockheed Martin, Atomico, and British Patient Capital.
Saville’s long-term goal? “One-click manufacturing”—a seamless workflow from digital design to finished metal part within hours.
If successful, that vision could reshape global supply chains—and put more “Made in America” labels back on critical industrial components.
Source: Fortune, June 26, 2025.